Premier Plant Hire is celebrating its 41st birthday this year. The Plant & Tool Hire company was founded in 1974 in East Dulwich, London and was always a reliable partner for the local builders and tradesmen. The equipment it provided to its faithful clients was of good quality, but its scope for growth was limited by its premises – a conglomerate of back-gardens in a side street and the semi-detached family home that was converted into a hire shop – and its outdated manual administration system. The business ambled along without any ambitions to reach much beyond the 3-mile radius it served. All of this changed when Paul Kuebler took over Premier Plant Hire in 2006. Paul, who grew up in Germany, had many years of experience running logistics operations in Europe and UK. “Having worked for all sizes of businesses, from family owned to large, global corporations, I decided to do something on my own. Premier Plant Hire was right up my street – having graduated in engineering gives me a thorough understanding of the equipment we provide and after all, hiring successfully is nothing but logistics: providing tools and machinery at the right place and time.” Overnight the company stretched its geographic scope by advertising its services on the internet. Being located at the centre of gravity within the M25, 5 miles from the city of London and 9 miles from the Olympic Site allows Premier Plant Hire to reach a market of 12 million people within 2 hours. “We started to advertise on Google and all of a sudden the calls came flooding in” remembers Paul the first months after establishing Premier Plant Hire’s web presence. Within a year the business progressed from being an insider tip amongst South London builders to providing lorry loads of scaffold towers to form the back-drop setting of the “Great Exhibition” the Royal College of Art set in scene to celebrate its 150th anniversary. The strength of Premier Plant Hire is everyone’s focus on customer service. The whole of the original team embraced the new vigour of the company enthusiastically. Roy Ebsworth, who has been working for the company since its foundation in 1974 sums it up: “All our customers are different and have their own ways of working. We know the people on site and we understand the constraints and pressures they face to get the job done and we do our bit to help them. Quite often, they face an unforeseen situation they need to address and we make sure we get the right tool to them – fast.” Since 2006 Premier Plant Hire grew by an average of 30% annually and two years after the change in management it was time to look for a new depot. Space is at a premium in London and finding bigger, affordable premises proofed to be a real challenge. As soon as Paul first set his eyes on the Giant Arches in Burbage Road, he knew that this would be the ideal base for the business. Being located only a mile from where the company operated for over thirty years means that none of the company’s clients have to go out of the way when they collect equipment, but the size and cut of the new premises opens a wide range of new opportunities. Chief Engineer Robert Clark is thrilled with the new workshop, which allows him to repair even large machines indoors. And Yard Manager Les Andrews is pleased with the prospect of having enough space to load 7 – 10 trucks simultaneously. The Administration Buildings comprise three offices of different sizes, one of which is used as the classroom of Premier Tower Training, the PASMA training centre from where Premier Plant Hire runs tower erection courses every second week. There is also a server room and staff facilities. The Admin Building, the Hire Shop next door and Premier Construction Academy were completely refurbished and decorated before the move and an electric central heating system has been installed. An Alarm System, which is linked to the police, has been fitted to protect the premises.
Since moving into the new premises, Premier Plant Hire invested into larger machinery and has increased its fleet of Bobcat excavators, currently ranging from 1.0t to 3.0t. “The diggers have been a real success and we usually only have a few hours to service them, before they go out on the next hire” states fleet engineer Robert Clark.
On the other side of the railway line are approx. 600m² of land, which also form part of the property. This area is waiting to be cleared and will offer enough space to realise the next ambition – Premier System Scaffolds will start soon to sell system scaffolds all over UK and there are plans to hire and assemble system scaffolds for clients in London and South-East England. Paul recently signed a deal with Premier’s new partners Tobler AG in Switzerland granting exclusive marketing rights for the products of Switzerland’s largest manufacturer of system scaffold. “System Scaffold is a tremendous opportunity in a country were you see only traditional tube & clamp scaffolds” enthuses Steve Creasy who just returned from Tobler AG’s head office in Rheineck, Switzerland, having spent a week of intensive training on this products. “Compared to traditional solutions it takes 30% – 50% less time and less than half the qualified labour to assemble a system scaffold.”
With Tobler, Premier chose an experienced manufacturer of scaffold, who started their business in 1995. The company grew fast from the word “go” and went international in 2003. Today Tobler produces its products in its own production plants and sells them in countries all over Europe, e.g. Austria, Bulgaria, Czech Republic, Romania, Russia, Switzerland and Turkey.
So what about setting up other depots in England? “We do not want to branch out over a multitude of depots – our ambition is simply to be the best provider of services to the construction industry in and around London” is the firm answer of Paul on this point. “Our strength is a close knit team that focuses on one thing only – customer satisfaction. Spreading an operation only distracts from this aim and I have witnessed to many organisations that got obsessed with themselves once they branched out.”
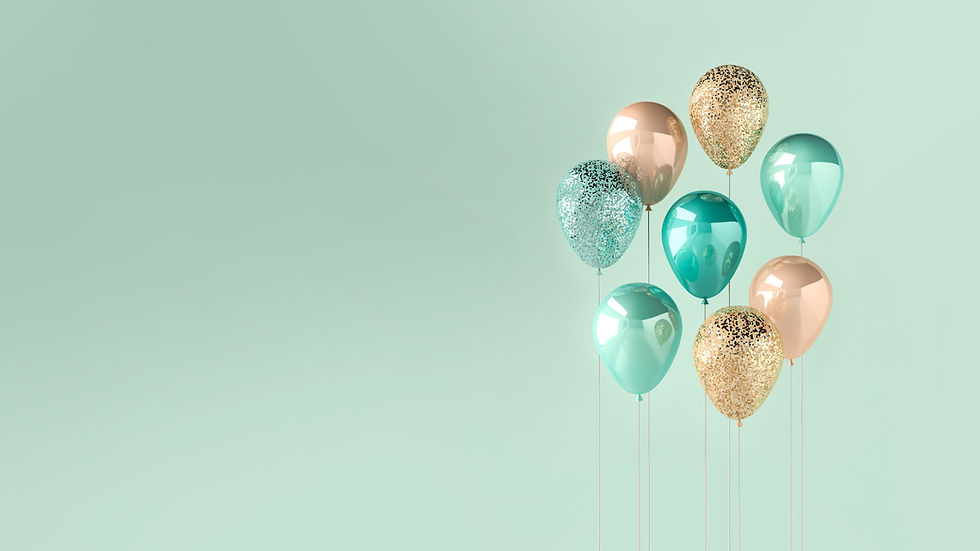
Comments